Article
What Is HAZOP?
18/07/2025
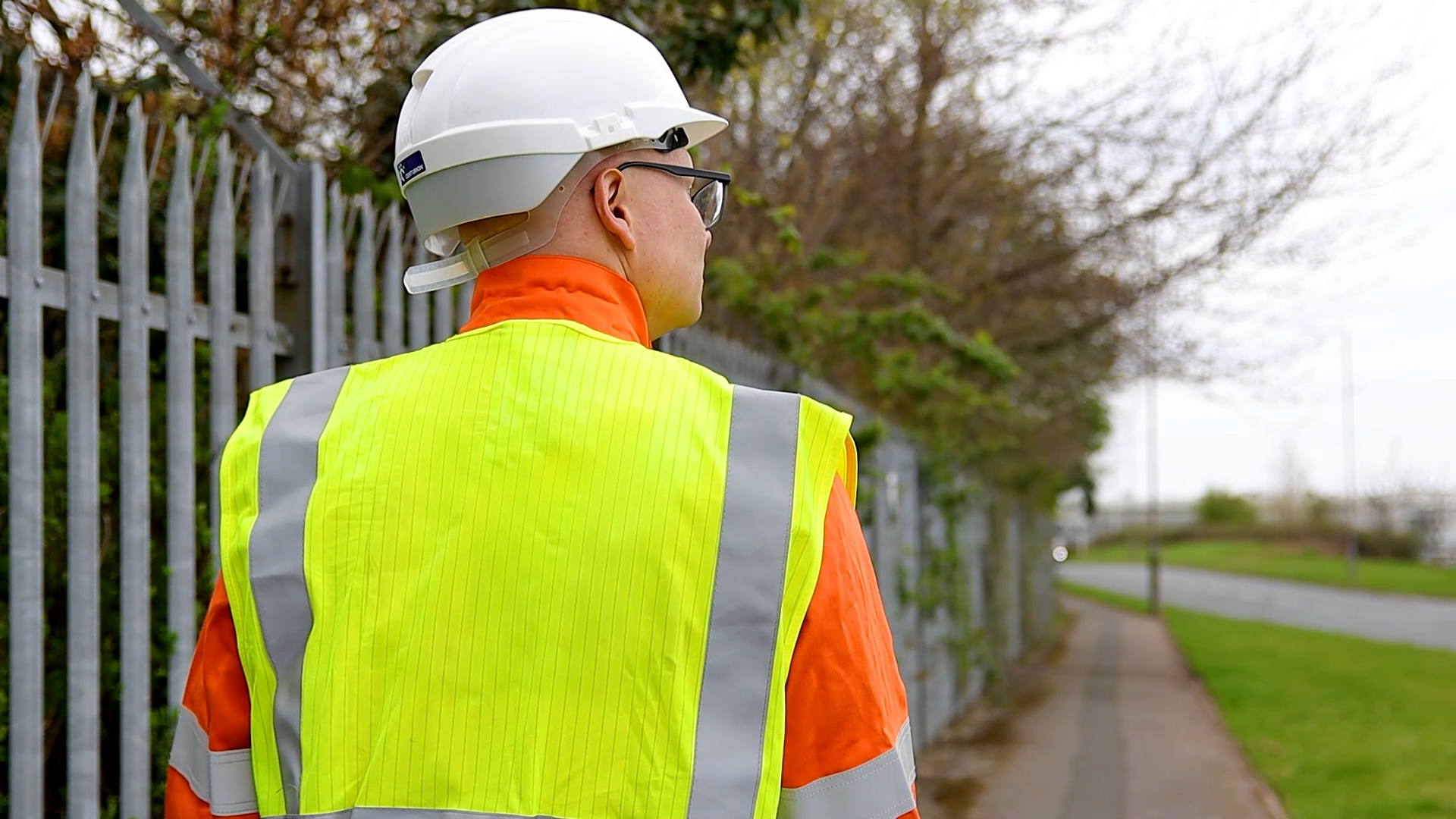
Processes involving hazardous materials, high pressures, flammable atmospheres, or extreme temperatures include inherent risks in their operations. When these processes involve complex systems, even a minor fault can quickly escalate into something far more serious.
Structured, formal risk assessment methods are critical in high-hazard industries to ensure all scenarios are taken into account and suitably assessed for the potential for harm. One of the most trusted and widely adopted techniques for identifying risks in the process and foundation industries is the Hazard and Operability Study (HAZOP).
Whether you’re implementing new processes, modifying existing equipment, or reviewing risks, HAZOP offers a reliable and systematic approach to identifying potential issues before they escalate into major incidents.
What Does HAZOP Actually Mean?
HAZOP stands for HAZard and OPerability. It’s a study which looks not only at the hazards inherently present in the chemistry or operation parameters, but also those introduced by operating whether your process be manually or automatically carried out.
HAZOP is a guideword-led , team-based risk assessment technique used to identify potential hazards and operational issues in process systems. It’s important to include members from a diverse range of engineering and safety disciplines to ensure there’s a breadth of knowledge in the room, minimise assumptions on behaviour of equipment, and ensure your study is as complete as possible.
HAZOPs are known as qualitative studies: the output is consequences and likelihoods assigned into bands according to a risk matrix as agreed by the group, but without the detail required to undertake design of further safeguards if required. Once the high severity scenarios have been identified in the HAZOP, these can be taken further into semi-quantitative or quantitative studies (such as LOPA) to allow the team to focus this higher level of detail and assign numerical values to failures where it’s most valuable.
These studies are conducted at many phases of a process lifecycle including during design, before construction or commissioning, to review an existing process or to understand the implications of modifications.
The main goal of HAZOP is to assess how a process might deviate from its intended design and operation, what could cause those deviations, and what the potential consequences could be. These deviations can be as a result of an equipment failure, maloperation or an upstream or downstream processes. HAZOP considers hazards, such as fires, explosions, and toxic gas releases, and operational consequences which can arise from equipment damage or process disruptions.
What makes HAZOP so valuable is its structured and collaborative approach. It uncovers risks that might otherwise be missed during less rigorous hazard assessments.
Where and When does HAZOP Apply?
HAZOP studies are typically conducted in industries where the consequences of a process failure could be severe. You’ll often find them used in sectors like oil, gas, chemicals, petrochemicals, pharmaceuticals, power generation, water treatment, food and beverage operations that involve pressurised systems, flammable substances, or reactive chemicals.
While HAZOP is a standard requirement for new process designs, it is also applied during plant modifications or after an incident highlights new areas of concern. Even sites which have not made major changes to their process operations are recommended to undertake HAZOP reviews regularly to capture smaller operation changes and ensure current operation continues to match the design intent.
Regulatory updates or changes in safety standards can also trigger a fresh HAZOP review to ensure that risk management measures are effective and appropriate.
The study can range from a single piece of equipment to an entire operation, depending on the scope and complexity of the business and can apply to batch or continuous processes, as well as installation of new processes or fully or partially decommissioning an existing one.
How Does HAZOP Work?
A HAZOP study involves a structured, guideword-led workshop led by an experienced facilitator. It is not a quick checklist exercise; it’s a thorough analysis of every part of a process system to challenge assumptions, identify hidden risks, and assess the effectiveness of existing controls.
HAZOP is based on piping and instrumentation diagrams (P&IDs), and this level of design detail is required as a minimum to make a worthwhile assessment. Earlier design stages such as concept or process flow diagram levels are more effectively assessed using other hazard study methods such as HAZID, which can support detailed design by highlighting significant hazard presence. HAZOP will then be able to tease out all the places hazardous scenarios may occur, on a design which hopefully goes a long way to addressing them and does not require substantial modification.
The process is broken down into smaller, more manageable sections called nodes. These could represent specific stages within the process. A clear process description is produced for each node with a high level of detail documented by and agreed with the assessment team before the hazard identification is undertaken. If you don’t know how the equipment is supposed to work, it’s very difficult to identify what can go wrong.
For each node, the team applies a set of guide words to prompt discussion about potential deviations.
Words like "No," "More," "Less," "Reverse," and "Other Than" are applied to conditions and used to explore how the process might behave differently from its intended design.
For example:
What is the consequence of NO FLOW through this pipeline?
What if we have MORE PRESSURE than we should in this vessel?
What happens if a material OTHER THAN the one specified is added by mistake?
For each deviation, the team identifies possible causes, assesses potential consequences, and evaluates existing safeguards. If gaps are identified, recommendations for improvements are developed and recorded.
HAZOP does more than identify risks associated with the presence of substances or use of certain equipment; it also examines operational issues. These might include equipment design flaws, limitations in control systems, and human factors.
All findings, actions, and responsibilities are formally documented in a HAZOP worksheet, providing a clear record for future reference.
Why HAZOP Matters in Risk Assessment and Hazard Identification
A thorough HAZOP study is one of the most effective tools for proactive risk assessment and hazard identification in complex process systems. It offers a chance to examine how a process could fail, what the consequences might be, and whether the existing protective measures are likely sufficient to prevent or manage those failures. For the high severity scenarios, this sufficiency will be assessed to a higher level of detail with a further assessment tool such as LOPA.
By identifying and assessing both hazards and operational issues, HAZOP reduces the likelihood of serious incidents, improves the reliability of operations, and ensures compliance with safety legislation and industry standards.
HAZOP promotes a safety culture where operational risks are openly discussed, assumptions are challenged, and decisions are based on evidence, not guesswork.
In high-hazard environments, this proactive, evidence-led approach can save lives, protect assets, and maintain your business's reputation.
Who Should Be Involved in a HAZOP Study?
One of the key strengths of HAZOP is the diverse range of expertise it brings together. The study is typically led by a qualified, independent facilitator and includes a team of people who are familiar with the process, the equipment, and how operations are conducted daily.
A well-rounded HAZOP team often includes process engineers, operators, maintenance personnel, instrument and control specialists, and process safety engineers. Bringing together a variety of expertise ensures that both technical hazards and day-to-day operational challenges are fully evaluated, resulting in well-informed, practical safety solutions.
How 6 Engineering Can Support Your HAZOP Needs?
At 6 Engineering, we work alongside your team to deliver HAZOP studies that aren’t only about compliance and legislation, they’re about making your processes safer, more reliable, and better understood.
Our experienced process safety engineers lead structured, focused workshops that encourage open discussion and gain valuable insights from the people who know your operations and design best.
We turn complex technical findings into clear, practical actions and records that improve safety.
Whether you’re developing a new facility, modifying an existing system, or reviewing how well current controls are managing risk, we’ll help you carry out a HAZOP study that’s thorough, actionable, and aligned with best practices.
If you’d like to arrange a HAZOP study or want to check whether your business needs one, get in touch!